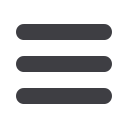

81
Maintenance of the timing belt on an 8 valve engine costs around
R$ 120, including labor. If you do not replace it at 40,000 km, the belt
can break. If it does, the valves and pistons, among other items, can
be damaged and corrective maintenance will include maintenance to
disassemble the cylinder head, bringing the total cost to about R$ 5,000.
These figures come from Roberto Barroso, commercial and
institutional manager at the Road Safety and Experimentation Center
(CESVI), and illustrate the importance of preventive maintenance. “Every
company that has a fleet and depends on it for the smooth running of its
business needs to have a regular vehicle maintenance program so that
it is never left in the lurch. In the case of rental and leasing companies,
this is critical: it must be part of the company’s culture and always be
included in the annual planning,” he stresses.
Preventive maintenance includes checking a number of items in vehi-
cles before the components fail - especially those that are worn out over a
given mileage, or which degrade over time, such as lubricating oil. Gene
rally speaking, each item has servicing and replacement intervals given
by the vehicle manufacturer - which are included in the owner’s manual.
The main items inspected are the suspension, brakes, tires, wiper
blades, engine oil, brake fluid, and coolants. “It is a simpler procedure
than it looks. But, oddly enough, there are many vehicle owners - and
companies that have fleets - that do not have a systematic program of
checks for such simple things as oil,” says Barroso.
When he talks about lots of many companies he is not referring
to car rental companies, which, in his opinion have a proactive attitude
that makes their business even safer, carrying out checks ahead of the
periods recommended by the vehicle manufacturers.
This is correct, says Barroso. After all, depending on way the cars
are used, some parts must be replaced before the end of their usual
working lives. “Shorter intervals between maintenance can be especially
positive for companies that have fleets that are used more intensely,
such as cargo carrying, constant driving on unpaved or steep roads,
used in mining, or just heavy traffic. This is the case, for example, for
car rental companies in cities like São Paulo, where traffic jams cause
wear and tear for lots of components,” adds Barroso.
Choice of workshop
| Equally as important as the maintenance
is the quality of products and services. Roberto Barroso recommends
that the company carefully assess the workshops they use. “An ideal
partner should have a portfolio of clients that the rental company can
analyze as a reference. If other reputable rental companies use their
services, it is a sign that provides peace of mind,” Barroso explains.
He adds that one of the workshop quality indicators that can be
checked is the certification.” And there another important reference.
One tip is to check if the workshop is approved by CESVI Brasil,” he says.
“IQA-CESVI workshop certification helps consumers and businesses
identify the establishments that offer quality technical services. The
approved workshops get an IQA-CESVI Certified Workshop seal. This is
valid for one year. Afterwards, it has to be reassessed, checking its level
of quality or showing it has evolved since the last analysis,” he explains.
When it finds a workshop it can trust, the rental company can even
transfer the management of its maintenance to it, controlling intervals and
costs. “For example, the workshop must notify the rental company about
when it needs to change the oil, or replace filters,” Barroso says.
Anticipating damage
Preventive maintenance can cost 40 times less than corrective maintenance and prevents long stays at
workshops. It is also important to choose the company that manages the maintenance of your vehicles
Para consultar a relação de
oficinas, acesse o site
do Cesvi Brasil:
To see the list of workshops,
please visit the Cesvi Brazil at
:
cesvibrasil.com.br/site.aspx/oficinas-certificadas
produtos e do serviço. Roberto Barroso re-
comenda que a empresa avalie muito bem a
oficina que fará esse trabalho: “Um parceiro
ideal deve ter uma carteira de clientes que a
locadora possa analisar como referência. Se
outras locadoras bem conceituadas fazem
seus serviços ali, é sinal de que dá para ter
tranquilidade quanto à qualidade dos servi-
ços prestados”.
Ele acrescenta que um dos indicadores
de qualidade da oficina, que o empresário
pode checar, é o aval de órgãos certificado-
res. “Eis aí outra referência importante. Uma
dica é verificar se a oficina está na relação de
reparadoras capacitadas segundo o Cesvi
Brasil”, aponta.
“A certificação de oficinas mecânicas
e de funilaria e pintura IQA-Cesvi contribui
para que consumidores e empresas identi-
fiquem os estabelecimentos que oferecem
serviços com qualidade técnica. As oficinas
aprovadas na avaliação recebem uma placa
com o selo Oficina Certificada IQA-Cesvi. A
classificação que a oficina recebe tem vali-
dade de um ano. Após esse período, a ofici-
na deve solicitar uma nova avaliação, na qual
pode confirmar seu grau de qualidade ou
demonstrar que evoluiu (ou retrocedeu) des-
de a última análise”, explica. Ao encontrar a
oficina de sua confiança, a locadora pode
até transferir a gestão da manutenção para
ela, que fica com a responsabilidade de con-
trolar prazos e registrar custos ao longo do
tempo. “Por exemplo, a oficina deve avisar a
locadora sobre quando ela precisa trocar o
óleo de seus veículos, ou sobre quando esti-
ver chegando a hora de trocar filtros”, sugere
Roberto Barroso.